Checking Out the Basics of Welding Evaluation: A Thorough Exam of Processes, Tools, and the Importance of High Quality Control in Welding Industries
Welding examination serves as a keystone in the maintenance of security and architectural integrity across numerous markets. Understanding the ramifications of these methods elevates crucial concerns concerning their effectiveness and the future instructions of quality assurance in welding.
Importance of Welding Assessment
Welding assessment plays an essential function in guaranteeing the honesty and safety of welded frameworks. It functions as a systematic method to examining weld high quality, recognizing potential defects, and making sure conformity with established standards and specs. The value of welding examination prolongs beyond plain adherence to policies; it is critical in guarding human lives and shielding investments in infrastructure.
Faulty welds can result in disastrous failings, leading to significant economic losses, injury, or death. Extensive inspection procedures are necessary to detect concerns such as insufficient penetration, porosity, or fractures prior to they rise into critical failures. In addition, reliable welding evaluation adds to the overall efficiency and long life of frameworks, ensuring that they can endure the problems for which they were designed.
In addition, the implementation of welding examination promotes a society of top quality and accountability within the welding market. By focusing on evaluation, organizations show their dedication to excellence, thereby improving their credibility and competition in the marketplace. Eventually, welding inspection is not simply a procedural step yet a fundamental element of engineering honesty and safety guarantee, essential for the effective implementation of welding jobs across different sectors.
Secret Examination Processes
An extensive method to welding examination entails a number of crucial procedures that are vital for ensuring weld high quality and structural integrity. The very first essential process is aesthetic assessment, which permits assessors to determine surface area issues such as cracks, porosity, and improper grain appearance. This technique works as an initial assessment to make sure that the weld fulfills defined standards.
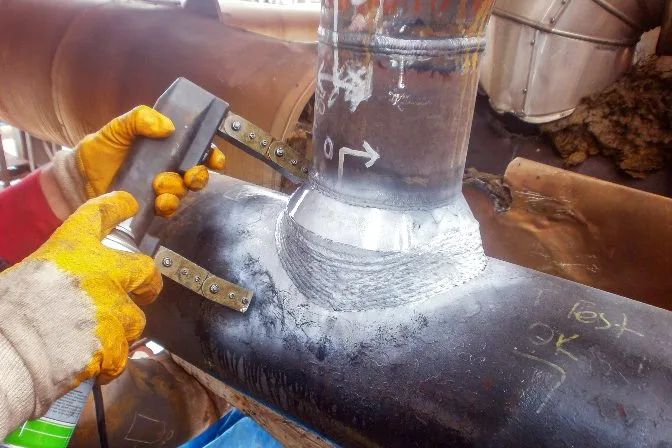
Additionally, damaging testing may be done on sample welds to evaluate their mechanical residential properties and performance under stress and anxiety. This procedure entails influence, tensile, and exhaustion testing to verify that the weld can endure operational conditions.
Lastly, documents and reporting are crucial parts of the examination procedure. Keeping accurate records of examinations, monitorings, and test results assists make sure conformity with industry criteria and promotes continual improvement in welding techniques. Jointly, these essential procedures create the foundation of efficient welding evaluation and quality assurance.
Tools for Weld Examination
Many tools are crucial for reliable weld examination, each made to evaluate various facets of weld high quality and efficiency. Among one of the most commonly made use of are visual examination devices, including magnifying glasses and view it borescopes, which enable examiners to determine surface defects such as splits, porosity, and incorrect combination.
Additionally, ultrasonic testing (UT) equipment is essential for identifying internal imperfections. This device uses high-frequency acoustic waves to disclose stoppages within the weld, making sure the integrity of the product. Radiographic testing (RT) tools, which use X-rays or gamma rays, in a similar way give understanding right into the inner framework of welds, permitting for the recognition of gaps or inclusions.
For specific dimensions, calipers and gauges play a significant duty in determining weld measurements and ensuring adherence to defined tolerances. Firmness testers review the mechanical residential properties of the weld, ensuring it fulfills performance requirements.
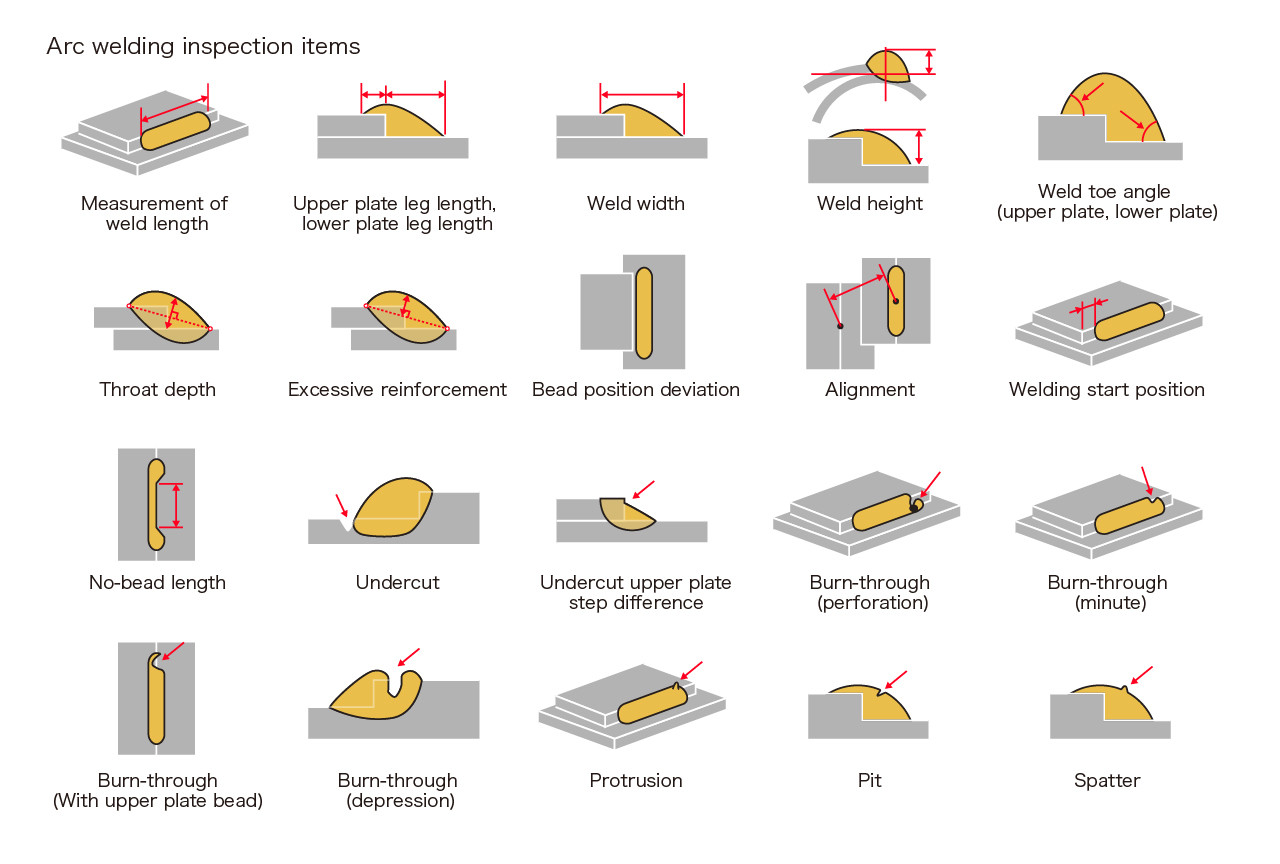
Methods for Analyzing Quality
Exactly how can the quality of welds be accurately examined? A variety of strategies are utilized to evaluate weld stability and make sure adherence to defined requirements.
Ultrasonic testing (UT) is one more prominent method that uses high-frequency acoustic waves to spot inner defects within the weld. Houston Welding Inspection. This technique supplies an extensive sight of the weld's stability without endangering its structural honesty. Additionally, radiographic screening (RT) employs X-rays or gamma rays to disclose internal flaws, supplying comprehensive insights right into weld top quality
Magnetic particle screening (MT) works for spotting surface area and near-surface stoppages in ferromagnetic products, utilizing electromagnetic fields and tinted particles to highlight problems. Color penetrant testing (PT) can be utilized to discover surface-breaking problems by using a color that seeps into fractures and is consequently revealed.
Compliance With Market Requirements
Conformity with sector standards is important for making sure the high quality and security of bonded structures. These standards, established by companies such as the American Welding Culture (AWS) and the American National Requirement Institute (ANSI), give standards that control the welding procedure, materials, and assessment methods. Following these criteria not just makes sure the architectural stability of welds yet additionally mitigates threats connected with failings that could lead to tragic repercussions.

Welding assessors are tasked with validating conformity with these requirements throughout the welding process (Houston Welding Inspection). This involves assessing welding treatments, checking welder credentials, and carrying out complete assessments of the end product. Non-compliance can cause considerable financial effects, job delays, and damages to a business's credibility
Furthermore, compliance cultivates a culture of high quality control within the company. By developing clear expectations and benchmarks, companies can preserve uniformity in their output and boost total performance. Regular training and updates on requirements are original site necessary to maintain workers educated and competent, making certain that all aspects of welding procedures meet or exceed regulative needs. Ultimately, dedication to industry requirements functions as a foundation for quality in the welding market, advertising safety and security and dependability in bonded structures.
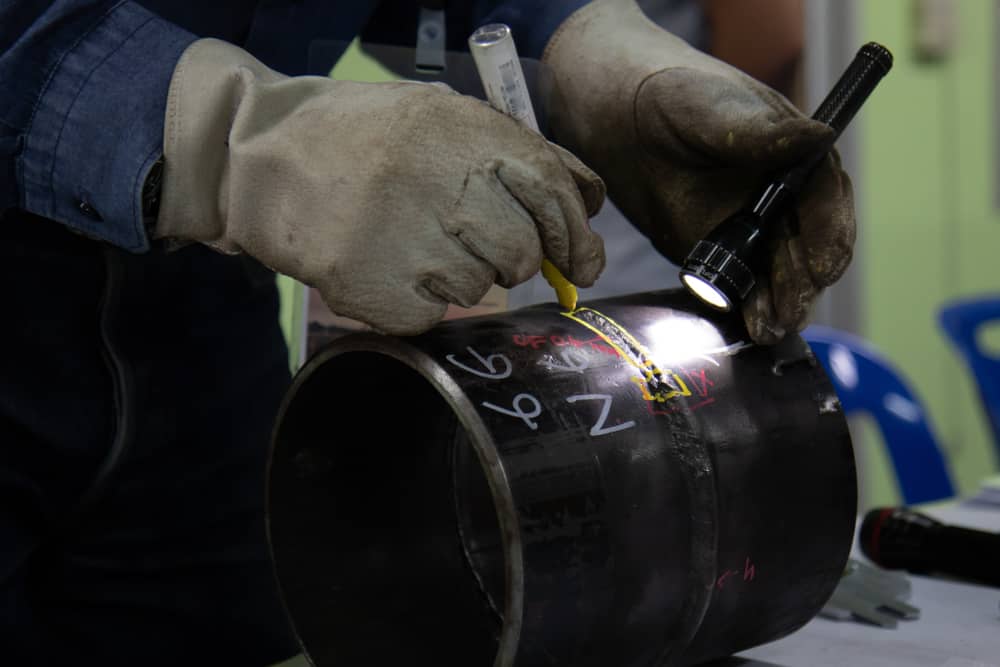
Verdict
To conclude, welding examination functions as an important part in keeping the safety and honesty of bonded frameworks. With the application of vital assessment processes and the application of sophisticated tools and techniques, possible problems can be identified and resolved properly. Adherence to sector standards ensures compliance and advertises a society of quality within the welding sector. Ultimately, strenuous evaluation techniques not just secure check human lives however likewise improve the longevity and efficiency of bonded buildings.
Furthermore, the implementation of welding inspection cultivates a culture of high quality and liability within the welding industry. Eventually, welding examination is not merely a step-by-step action but an essential part of design integrity and security guarantee, essential for the successful implementation of welding projects throughout different markets.
An extensive approach to welding examination includes several essential procedures that are crucial for ensuring weld high quality and structural stability. These criteria, developed by companies such as the American Welding Culture (AWS) and the American National Standards Institute (ANSI), offer guidelines that regulate the welding procedure, products, and assessment protocols.Welding examiners are tasked with confirming conformity with these requirements throughout the welding procedure.